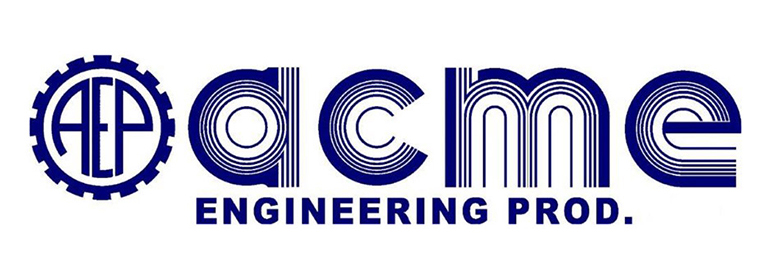
The Company
ACME Engineering Products is a family-owned manufacturing company created in 1956. It boasts design, mechanical, electrical and electronic skills and has grown with the talent of its employees and their commitment to the organization. It offers the following range of products:
- Gas detection system for air quality control of buildings, especially garages;
- Boiler systems for commercial and industrial installations;
- Self-cleaning scraping strainers for sanitation of water intakes, process liquids and wastewater.
The Situation
Leadership has undertaken several actions in terms of productivity, technology and skills development. In recent months, several new contracts and customers in need of renewing their system have been added to the order book and they continue to come in.
Indeed, ACME is currently experiencing sustained growth and is facing several challenges in order to maintain this growth; one of the most important being the management of human capital in the gas detection department. More specifically, Leon Karanfil, the Product Manager of gas detectors, announced that he was retiring on June 30, 2018, after 36 years in the company. ACME contacted HumEng when it was midnight minus one to implement a successful transition.
Indeed, following a needs analysis with HumEng's skills development consultants, the urgency of the need to plan Mr. Karanfil's succession became evident: ACME had to quickly set up simple knowledge transfer structures to limit the impact of the departure of a large part of Mr. Karanfil's knowledge and ensure business continuity.

Production Workshop - Gas Detection
The Solution
To address this challenge, HumEng proposed an approach that included the following steps:
- Document and transfer critical knowledge of the process of designing, manufacturing, delivering and supporting gas detection systems;
- Enhance the understanding of the organization and the process for managing the different steps involved in the delivery of a gas detection system;
- Increase the level of skills and controls to deliver gas detection systems on time.
Project Execution
The project began with the development of documentation on the process of design, manufacture, installation and support of gas detectors and its critical points. Each skill was then assigned to a person responsible and to a second person in order to have an additional resource for vacations and in case of emergency or illness. This was carried out in collaboration with management.
HumEng consultants then supported the development of documentation of critical working methods, both at the level of quotes, start-up of orders, invoicing and on the technical side for the production of simple or complex units. Following the validation of the standard work procedures, the implementation steps followed:
- Develop a training guide including the documentation and a trainer's guide;
- Support the deployment of skills recognition and on-the-job training;
- Implement simple tools to track the progress of skills transfer and the training process.
Quickly Visible Results
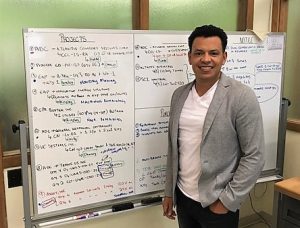
Christian Morales, new Head of Operations at ACME Engineering Prod. Ltd
- Productivity and efficiency gains achieved in a context of change;
- A process clearly established and accepted by the team;
- Procedures developed according to critical skills that can quickly be used in production;
- Skill profiles with clearly established tasks assigned to the best employees for efficiency and performance;
- Employees involved in the change process;
- Resistance to change minimal;
- A new Head of Operations, quickly trained with information on the company's context, tools and procedures to continue Mr. Karanfil's work and support the company with the coming technological changes;
- Issues raised and challenges, ignored for too long, identified.