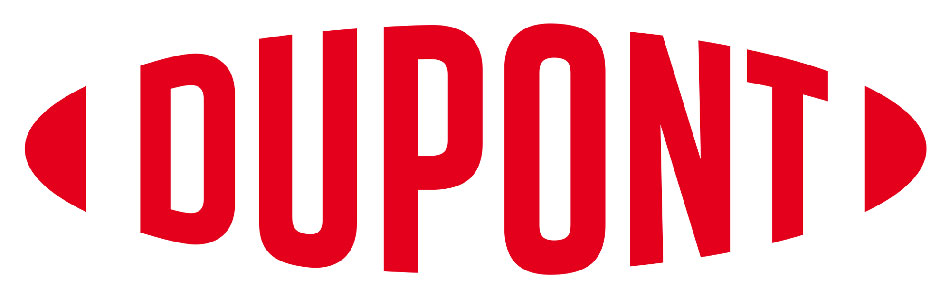
The Company
DuPont specializes in chemistry, plastics and adhesives. It is divided into the following five categories:
- Electronics and communication technologies;
- Execution materials;
- Colour coatings and technologies;
- Safety and protection;
- Agriculture and nutrition.
DuPont has several plants around the world, including one in Thetford Mines that specializes in the production of agglomerated quartz slabs.
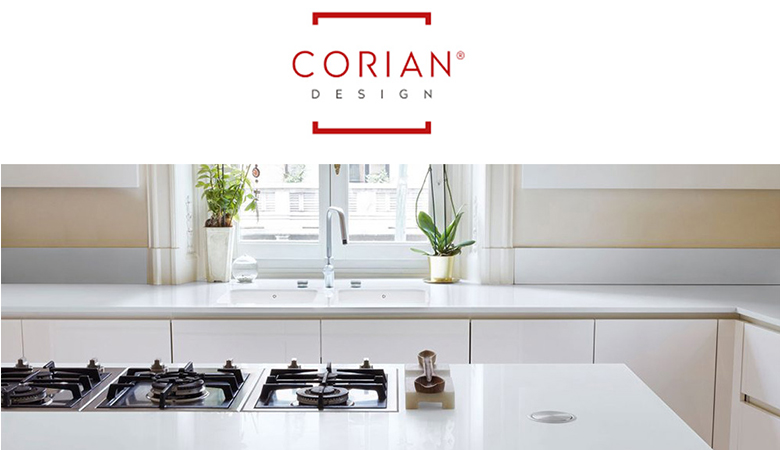
The plant has about a hundred employees and is challenged with the prospect of several retirements within its maintenance team.
The Situation
DuPont wanted to modernize its training system in order to optimize:
-The prioritization of investments;
-The dissemination of training;
-The evaluation of impacts and efficiency.
HumEng started working with DuPont about fifteen years ago. At that time, a knowledge-based training system aimed primarily at operations was implemented. Given the current business environment, the plant wanted to be able to do more with less.
Proposed Solution
HumEng proposed a multi-phase solution, covering the two main areas of operations and maintenance. Three main themes for action were selected:
- Optimize the training process;
- Modernize and simplify critical training tools;
- Integrate and mobilize stakeholders.
Phase 1: Structuring the Training
Operations
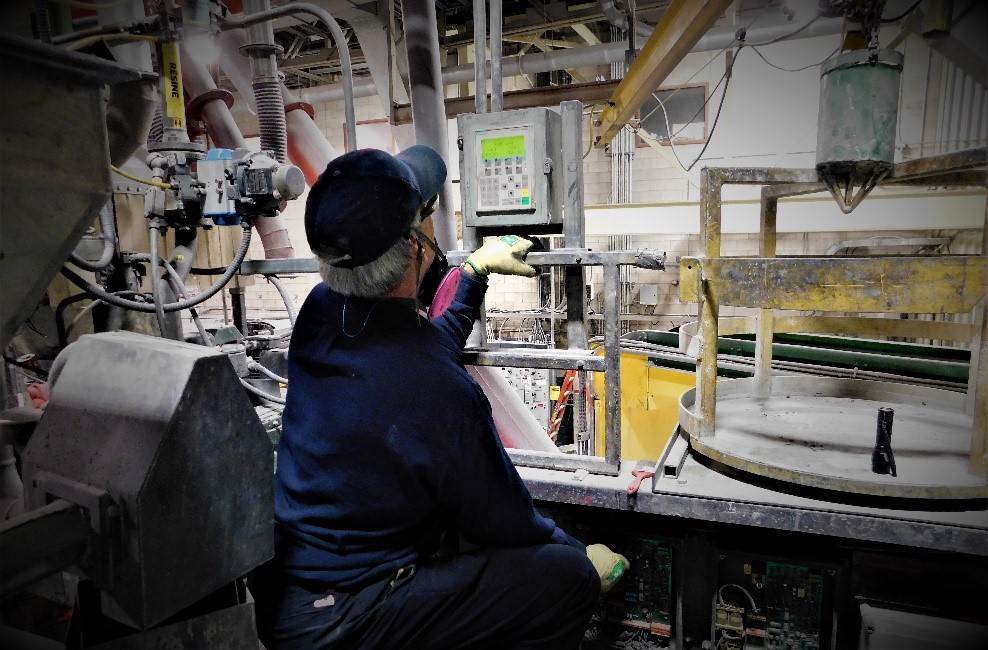
The Maintenance Team at work at DuPont Thetford Mines / HumEng Photos
Operations especially needed training on equipment, more specifically on the press, whose main equipment had recently been changed.
- Identification of critical skills;
- Creation of learning paths for each position;
- Creation of learning paths for each position;
- Creation of a training module on the slab production process, including an overview of the different sectors and a summary of the function of the main equipment;
- Modernization of critical existing training tools.
Maintenance
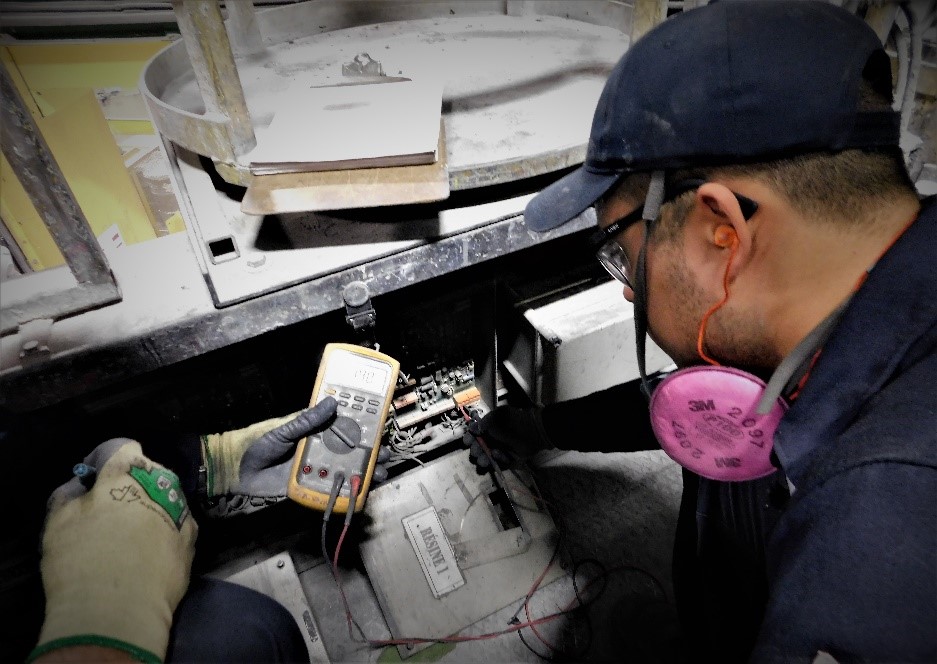
The Maintenance Team at work at DuPont Thetford Mines / HumEng Photos
The maintenance sector, on the other hand, mainly needed to harmonize the level of basic knowledge in mechanics, electricity and instrumentation, to structure on-the-job training and to standardize know-how related to maintenance procedures.
- Identification of critical skills;
- Creation of training paths for each position;
- Validation of basic knowledge on several topics related to industrial mechanics;
- Updating some of the knowledge among maintenance employees;
- Development of standard maintenance procedures on critical equipment, in order to prevent accidental breakage, reduce rejects and extend the life of equipment parts.
Implement Training
The skills management-based training approach targets training development efforts on critical elements that account for about 20% of skills. This approach makes it possible to free up resources allowing an implementation that promotes skills transfer and the return on expectations.
- Creation of a governance committee;
- Coaching of supervisors;
- Deployment and analysis of the results of maintenance knowledge and skills assessments;
- Implementation of priority e-learning modules in maintenance;
- Implementation of online training in operations;
- Learning of practical skills with learning paths through on-the-job training;
- Selection of trainers;
- Training of trainers.
The implementation of the solution was closely monitored by the HumEng team using punctual follow-ups, in order to help DuPont achieve its objectives.
Measurable Results
Following the implementation of the solution, several measurable results were observed. At the level of the skills development and management structure, the following concrete results were achieved:
- 6 certified on-the-job trainers:
- 4 in production and 2 in maintenance;
- Their status is included in the collective agreement;
- Learning paths allow to measure the progression of critical skills on a monthly basis;
- The approach has allowed for the development of individual training plans;
- The plant targets production problems and develops specific training tools.
Finally, results directly related to the plant's performance were observed. More specifically, the approach contributed to:
- Reduction of rejects from 10% to 4%;
- Reduction of maintenance time by 40%;
- Increase in the life of equipment:
- Conveyor belts: 40%;
- Pump: 30%;
- Calibrator: 50%.