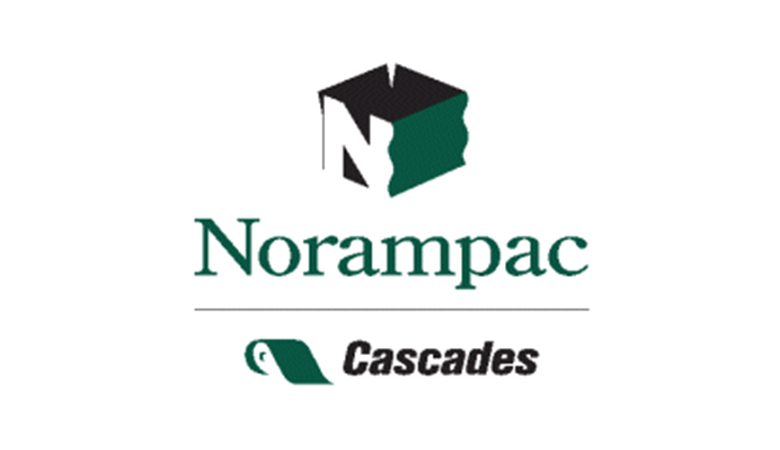
Context
Norampac, Cabano mill requests HumEng’s help to implement a training infrastructure for its paper machine operators. They want to actively participate in the process and become more autonomous in the development of training documents (standard operating/maintenance procedures) with their key operators.
Our Proposal
Taking into account the mill’s objectives, HumEng proposes the following activities to support the implementation of the training infrastructure for operators:
- Production of skill profiles for key positions;
- Identification of training aids to be developed to support the critical skills of the job profiles;
- Production of eLearning activities on papermaking (generic);
- Production of standard operating/maintenance procedures (mill best practices);
- Coaching of management, first line supervisors and trainers on the training process and their responsibilities.
Action Plan
Mixed strategy with the utilization of eLearning, standard operating/maintenance procedures and structured on-the-job training.
Some Results
- Implementation and follow-up of the elements of the program (mentor availability, E-learning hours, up-to-date documentation) are more disciplined and organized;
- For a comparable investment, Norampac has more training time, full-time mentors, availability of E-learning modules, updated procedures and support documents, etc.;
- Documented procedures that allowed for the standardisation of work practices;
- Theoretical knowledge greatly improved the comprehension level of operators and troubleshooting skills;
- The total training time for a job is similar to what it was before the project, but operators are now much more competent and efficient during interventions;
- Training of operators is followed-up and documented;